Pranab Kumar Bhattacharyya
Founder – AI Chat Rubber Polymers, Pune, Maharashtra, India

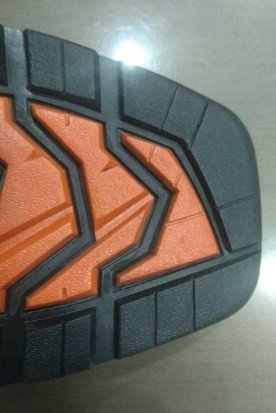
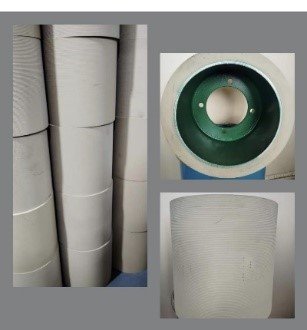
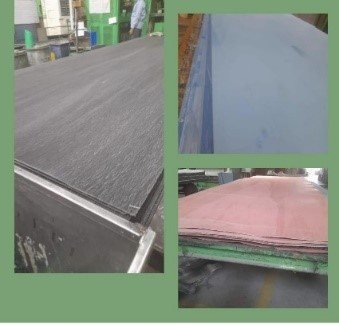
Introduction
NBR rubber is extensively used in various industrial applications. Typical Nitrile rubber applications are belting, sheeting, cable jacketing, hose for fuel lines and air conditioners, sponge, gaskets, arctic/aviation O-rings and seals, precision dynamic abrasion seals, and shoe soles. Other automotive applications are engine gaskets, fluid- and vapor-resistant tubing, fuel filler neck inner hose, fuel system vent inner hose, oil, and grease seals. Nitrile powder grades are used in window seals, appliance gaskets, footwear, cable covering, hose, and friction material.
Composites such as brake linings, and food contact applications.
- In the 1990s, the use of asbestos gaskets was banned due to the toxic nature of asbestos. To fill this void, non-asbestos gaskets emerged as a safer alternative for various industrial applications. Non-asbestos gaskets find their use in a wide range of industrial settings, including Air Compressors, Diesel Engines, Marine Applications, Power and Utility, HVAC Systems. Material Handling and Pipelines. Pipeline gaskets play a crucial role in sealing pipeline connections and preventing leaks in oil and gas transportation. A typical export-oriented compound requires not only chemicals that provides good stiffness and permeability but also requires low temperature properties through series of tests. Such formulations typically require special fillers like Kevlar, paper pulp, Rockwool, polyester staple fibres, cellulose derivatives, coated powder and so on besides white fillers like China clay, calcined clay, Silica and curatives. A suitable polymer blend is required for providing process friendly compound, suitable under oil and gas environments.
- Rice, as an agricultural product, requires the removal of its husk to become commercially viable. Two main types of machines are commonly used for husking: impeller type and rubber roll type machines. In impeller type husking machines, rice is scattered and husked by the impact of collision with an external surface. While these machines are effective, advancements in rubber roll technology have led to a preference for rubber roll huskers. In these machines, paddies are fed between two rubber rollers, and the husk is removed due to the high friction generated between the paddy layer and the outer surface of the rubber rollers. The rolls in husking mills require exceptionally high hardness and modulus values. Traditionally, achieving the necessary hardness and modulus was accomplished by using high amounts of non-black fillers and sulphur. However, this approach often resulted in poor processability during mixing, inconsistencies in batch quality, reduced elasticity, and diminished heat resistance. To address these issues, modern formulations have incorporated special resins. These resins improve the processing characteristics, enhance the service life of the rubber rollers, and maintain the required hardness and modulus without compromising other properties. This chapter provides detailed formulations for both traditional and modern approaches, ensuring that you have the information needed to choose the best method for your specific requirements. Automotive industries.
- Cork Rubber material is a combination of first grade granulated cork and a synthetic rubber polymer. This gives the product the high resilience of rubber and the compressibility of cork. Nitrile Rubber Bonded cork gaskets are Transformer and mineral oil resistant having good compressibility, above 80% recovery after compression, very good compression set properties, very good impact, anti-slip shock absorbing properties. These gaskets are widely used industry, heavy electrical industry, ship building industry , railways and aircraft industry. In this chapter our focus remains on compounding and formulation of Cork Gasket type RC 70C
- Shoe Soles in NBR rubber are used for industrial applications and tested against mineral oils and fuel resistance properties. Formulation of NBR shoe soles based on high ACN content rubber for better fuel and oil resistance properties has been given with special consideration of high heat resistant and high hardness moulding friendly compound minimising chances of cracking during removal from mould at hot condition.
This chapter focuses on formulations for specific consumer sectors, with an emphasis on processing, use, and customer base. Compound designer should focus on Process Failure Mode and Effect analysis during designing of compound so that developed compound should be process friendly to produce defect free products
The chapter covers the following topics of discussion
- General specifications or requirement of properties based on application,
- Typical method of processing.
- Reason behind selecting the grade of rubber and type of materials suitable for a successful compound
- Procedure of Mixing of chemicals in two roll mill or Kneader with typical processing parameters
- Troubleshooting related to compound design for defect free products
- Typical formulations closely related to industrial applications.
Disclaimer: While the formulations provided here are representative of industry practices and closely related to product development, AI Chat Rubber Polymers assumes no responsibility for their commercial success. No compensation or claims can be made by any industry or individual based on these formulations. Please also refer the terms of using the website applicable to all contents described or written herein.
(The complete chapter is available in Member’s area)